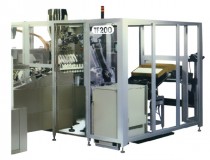
The tube filling and sealing machine is made to handle tubes like aluminium collapsible, lami or coextruded plastic tubes. These machines are very well protected but can be easily accessed. The free bearings mechanism of the machine does not require any maintenance.
The vacuum emulsifying mixer is a very powerful machine used by pharmaceutical companies for their product filling solutions. The strong force of the emulsifier or the homogenizer created by its high speed lets the feed material to go through the narrow head of the machine thus generating a strong circulation.
The vacuum emulsifying mixer is used to blend, emulsify, mix and homogenize the product in the vessel. This leads the cream products to increase their stability, lustre qbd smoothness. These machines have amazing ability to mix water and oil phase to give rise to perfectly emulsified products. The machine also has a vacuum-resistant jacket and is equipped with a high speed homogenizer and scraper. The vacuum pump aided to the machine brings the air bubbles out of the mixed product thus extending the storage time of the same.
The capsule polishing machine offers you a low cost solution to your drug cleaning problems. The state-of-the-art capsule cleaner is a perfect companion to the semi automated or automated capsule fillers giving output of 400,000 capsules per hour.
The machine parts include a hopper, a vibrator and a drug powder collector which are all made up of permissible materials to enhance their durability. The polishing section consists of two chambers made up of stainless steel that are fitted with a filter cloth.
The process is relatively very simple. The uncleaned and the unpolished capsules are gently conveyed through the capsule polishing machine by a soft nylon rotary brush. The brush very carefully rubs the capsules and cleans away the dust from them. The machine is also attached to a vacuum mechanism to carry away the debris generated as a result of the polishing. The process occurs as a batch operation.