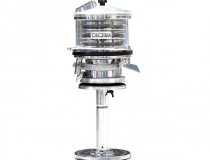
The pressed pharmaceutical tablets are ridden of the dust particles aided by vibration and air pressure. Most of the machine components are made of 316L stainless steel or white derlin which are very durable. The tool is innovatively designed given to the fact that the head can be easily removed in the form of a complete unit after the release of every two latches. This helps to quickly interchange when moving from one product to another and also helps in easier cleaning. The window mechanism also helps you to visually inspect the products and open the swings for sampling the tablets.
The non-complex structure of the tablet duster lets you to easily remove the motor section from the base by pulling just the interlock pin beneath. The three-leg base keeps the machine at level and allows flexibility while fitting it next to the tablet press. There is also a provision for vacuum attachment for collecting dusts. The compact entry and exit of the machine allows the use of large totes. This also ensures that the tablets can be inserted into the unit from any side with 360 degree adjustability.
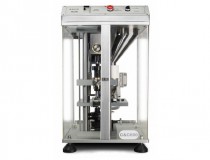
In a typical operation of the tablet press, the first step includes the bottom punch being lowered into the die thus creating a cavity into which the feedstock is fed. The excess is scraped and the lower punch is temporarily brought down to avoid spillage. After the upper punch is drawn downwards into contact with the powder, a compression force is delivered by high compression rolls thus fusing the granulated material into a hard tablet.
Follow On:-
No comments:
Post a Comment